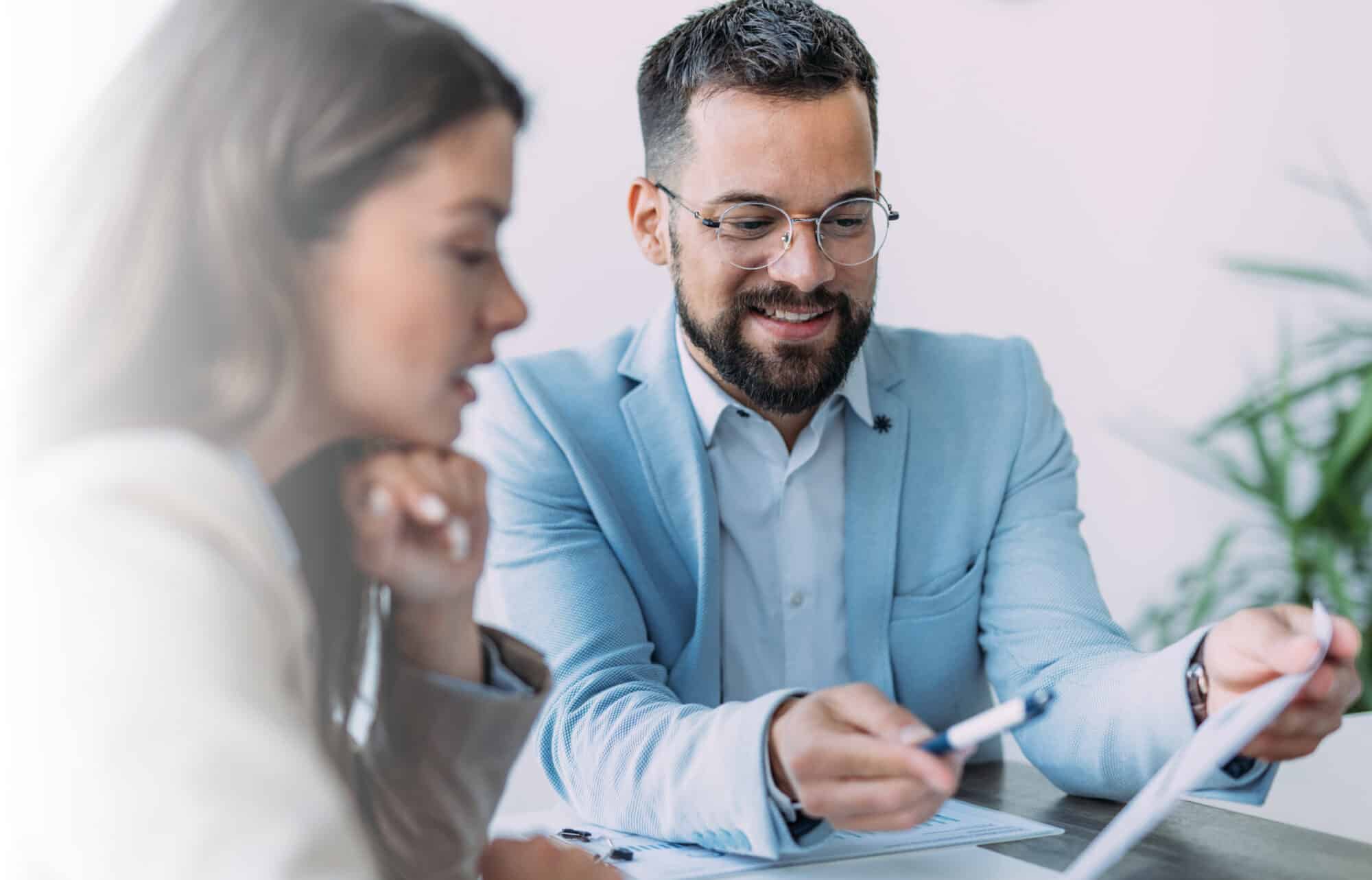
Home / Services / Manufacturers / Product Recall / Live Recall Management
Recall Incident Management
Do you have a product or component that you need to recall? Struggling to know what you need to do to get your product back and communicate with your customers? Don’t have the resource to manage the recall on your own?
With our experience of assisting with over 1500 actual product incidents, RQA Group can help you manage your recall from end-to-end and help you get back to business as usual as quickly as possible
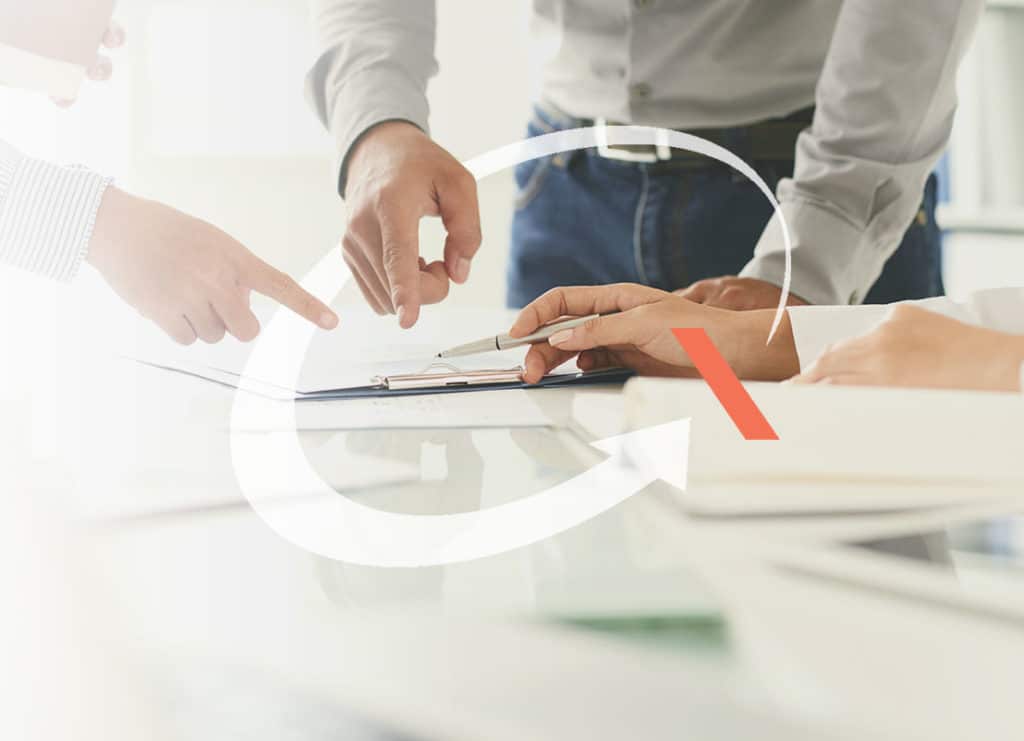
The following services are all modular. They can be provided as stand alone or together as part of a larger programme – we are flexible to your needs. These are just some of the ways we can help in the event of a recall, if in doubt please get in touch to discuss your needs and find out how we can help you navigate a recall.
Risk Assessment
The first step is evaluating the risk to consumers in order to understand if a recall is necessary, and if so how urgent the recall may be.
Our consultant will evaluate the risk to a consumer and work out the steps that might lead to injury
- We use internationally recognised methodologies for risk assessment such as RAPEX, PRISM and Nomograph
- This helps a company put the nature of complaints in context and understand the severity of the risk
- Conclusion could be that the risk is low and no action is required
- Conclusion could be that the risk is moderate or high and action is required
Based on this risk assessment an action plan can be developed for the next stage.
Replacement programme
If you do need to get your product or component part back, RQA can assist you to make consumers aware who have bought the product or faulty part involved in the replacement programme. We can also set up methods for them to check if their specific product has an issue.
- Recall Website: we can set up a website – in multiple languages – where a customer can input a code and check if their product is part of the recall action, fill in their details and request a replacement part
- We can send consumers replacement parts, anywhere in the world
- Translations: we can translate websites and emails into the many languages for the consumers
- Call centres: we can set up call centres using local numbers covering multiple languages
- We can proactively contact consumers as well using contact lists provided by retailers / warranty information
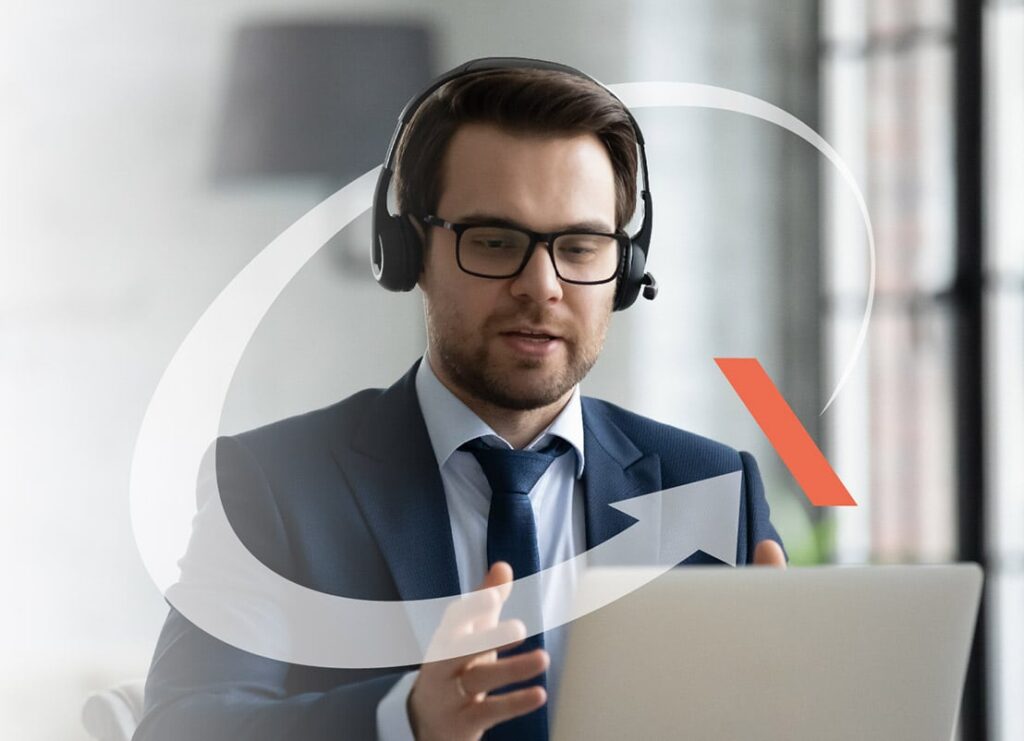
Storage and Destruction
Getting your products back, minimising the loss, and securely destroying the affected goods is a real challenge during a recall. Even having warehouse space and ensuring the returned parts are quarantined can be a real issue for companies in a recall.
- RQA can organise storage and warehousing around the world for replacement parts or faulty parts that are sent back
- We can assess goods in warehouses to sort “good” from “bad”
- Finally, we can also arrange product destruction under authorised and certified methods
These are just a few of the services we can offer in relation to managing a recall, and of course many unexpected issues usually come to light during the course of the recall, which we can help you manage. Click below to contact us and find out more.
We provide services for:
“De’Longhi Group has been working with RQA for several years now, always finding it very beneficial to the company, teams and people. High professionalism, prompt and competent interventions, have provided great benefits and contributions to continuous improvement of our processes, the strengthening of a preventive approach to potential crisis, and effective training. A very successful cooperation indeed!”
Lorenzo Paglierani,
Group Product Safety & Liability Director, Delonghi Group
“I would like to thank RQA for the amazing job! The crisis simulation went very well and the observations provided in the report were extremely insightful.”
Francesco Giliotti,
Legal Vice President, Group DPO, Group Crisis Team Coordinator
Barilla S.p.A.
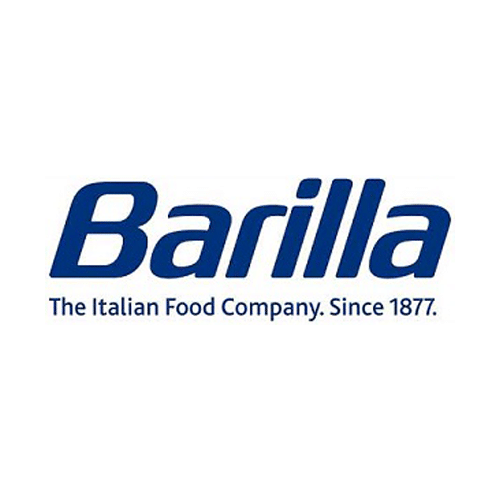