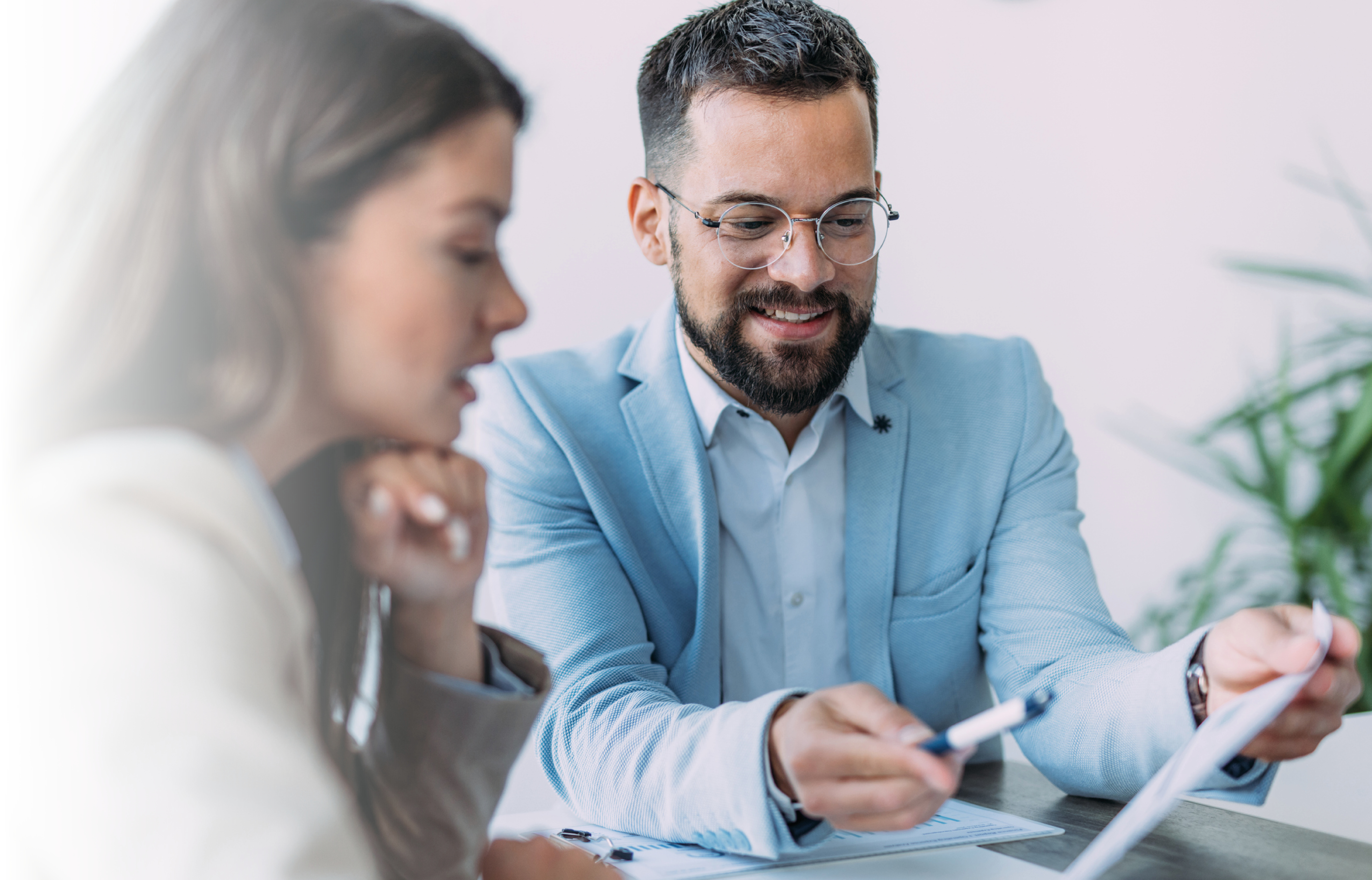
Crisis Consultants
RQA offer expert advice and services to product recall insurers and their policyholders as retained crisis consultants, through our premium offering which includes:
- 24/7 product recall incident support
- Pre-incident risk management consultancy and training for insureds
- Risk engineering reports and support to assist underwriters and claims teams
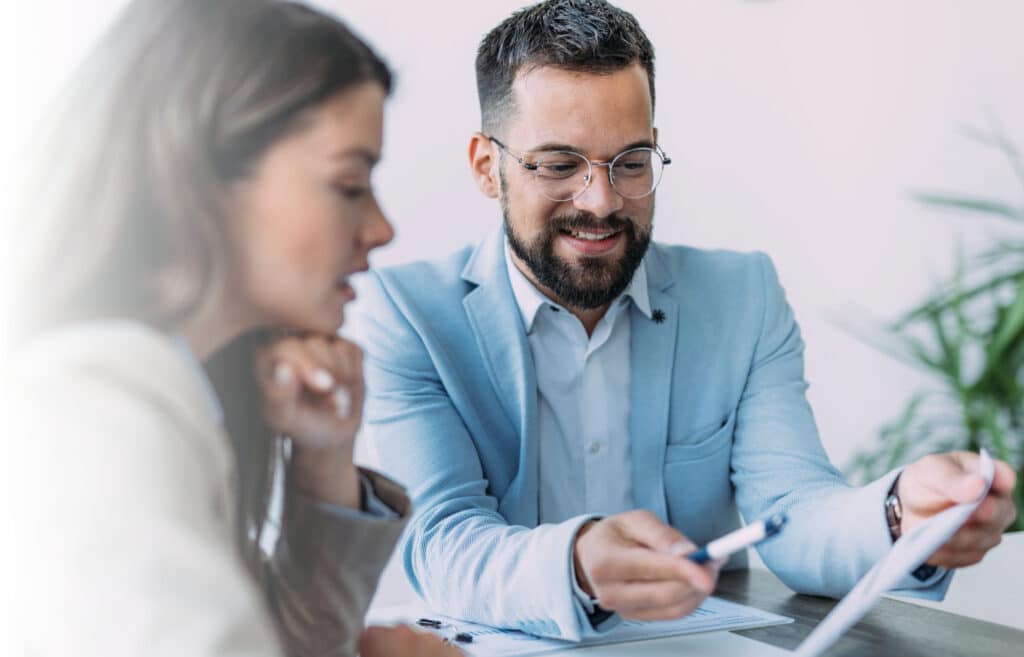
Product Recall Incident Support
A key service for our insurance clients is to provide incident support to companies who have contamination or product recall insurance.
In the event of a call to the dedicated incident line, RQA will put the client in touch with an expert consultant. They will provide any support that is necessary in order to help the insured get through the potential crisis situation by helping them to understand the scale and severity of the issue, defining the regulatory compliance, and then assisting them in developing an action plan and executing any necessary market action. RQA has advised on well over 1500 product fault or product recall incidents. A few examples include:
- Glass in food
- Faulty electrical equipment
- Reports of injuries caused by a wide range of consumer goods
- Chemical contamination of products
- Under-performing industrial equipment
- Consumer complaints with mobile phone accessories
- And many, many more…
In our experience, some insureds like to have external experts to act as a sounding board and to challenge the already developed approach, others need help in a specific area, and others are inexperienced or unprepared and need maximum guidance and support.
RQA can cover this range of client support requirements. Of course, the specifics of all responses are different, but many include some of the following:
- Investigation to understand the cause of contamination or product fault
- Analysis of the contaminant or unknown material
- Visit suppliers who may be involved in contamination
- Root cause analysis / FMEA
- Risk assessment methodologies
- Advice on communicating incident to stakeholders and recall execution
- Development of crisis communication strategy
- Reviewing action so far and discussing possible next steps
- Set up call centre capability to provide information to consumers in response to major public recall
- Advice on traceability to narrow recall scope
- Development of action plans and crisis capability
- Collection of suspected contaminated product from consumers
- Involvement of specialists in malicious tampering / extortion cases
- Withdrawal of products from stores
Pre-incident Risk Management Consultancy & Training
Underwriters will often allocate a risk management budget for the clients to use for RQA services to focus on improving the insureds’ safety, quality and recall systems and procedures. Examples include:
- Following a recall caused by a contaminated ingredient from a high risk supplier RQA were asked by the product recall insurer to assess procurement management systems to evaluate the effectiveness of supplier approval procedures and ensure only approved supplier can be used. The objective was to reduce contamination from incoming ingredients.
- RQA visited multiple sites within the same company to investigate foreign body contamination risks and ensure the same procedures and controls are adopted across all sites within the business.
RQA has a full range of services to assist companies in reducing the risk of product recall as well as improving their capability in management of recall. Click here for more.
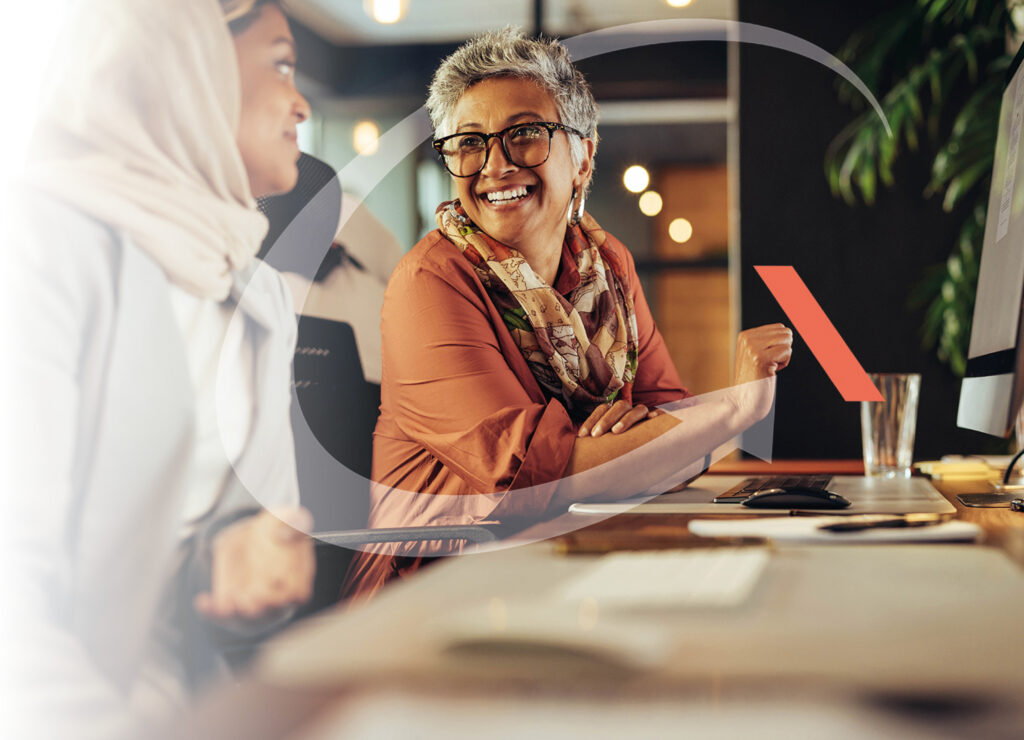
Risk Engineering Reports & Support
RQA consultants write many confidential reports for underwriters, on particular submissions, a product type or a sector in order to assist the underwriter in evaluating the risk of underwriting a company, or expanding their scope to other products and even sectors. A few examples include:
- Best practice in metal detection to minimise the risk of recall due to foreign body contamination
- Assessment of specific food categories and their recall risk and key recall prevention strategies
- The efficacy of novel processing techniques in eliminating pathogens and reducing contamination
- Risk assessment report on effectiveness of a company’s systems in preventing contamination and product recall
- Approaches processors should take to control the risk of salmonella in eggs
- The effectiveness of tier 2 and 3 automotive suppliers in managing their supplier to reduce component failure
- Defining risk levels related to product recall for food and non-food products, ingredients and components
We have also advised on the most appropriate questions to include in the product recall insurance application form; focusing the forms to ensure the right questions are asked in as concise a manner as possible. We have advised on sector-specific product recall insurance application forms, for example in automotive.
Click here for more on our risk engineering support and reports available to purchase.