We provide services for:
How can RQA help you?
We work globally with product recall insurers, manufacturers and law firms, helping organisations avoid product safety issues and be ready to
react effectively when crisis strikes.
RQA has a proven track record with 25 years’ industry experience and we are trusted by some of the world’s biggest brands.
- Extensive global network of over 120 experienced consultants
- Our Plan Train Test philosophy is purpose-built for today’s risks
- We work with you to build a robust product safety strategy
- We can help your business recover when a crisis occurs
Trusted by leading brands
“De’Longhi Group has been working with RQA for several years now, always finding it very beneficial to the company, teams and people. High professionalism, prompt and competent interventions, have provided great benefits and contributions to continuous improvement of our processes, the strengthening of a preventive approach to potential crisis, and effective training. A very successful cooperation indeed!”
Lorenzo Paglierani,
Group Product Safety & Liability Director, Delonghi Group
“I would like to thank RQA for the amazing job! The crisis simulation went very well and the observations provided in the report were extremely insightful.”
Francesco Giliotti,
Legal Vice President, Group DPO, Group Crisis Team Coordinator
Barilla S.p.A.
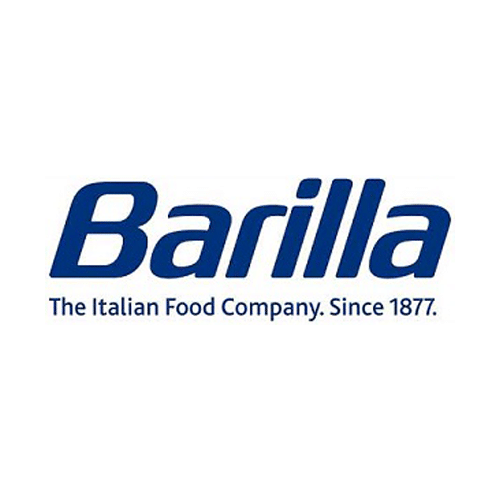